ピンインペースト(Pin-in-Paste、別名:Through-hole Reflow)とは、スルーホール部品(ピン付きコネクタなど)をリフローはんだ付けで実装する手法です。
従来、リード付き部品はフローはんだや手はんだ工程で実装していましたが、この技術を用いることで、表面実装(SMD)と同一のリフロー工程内でスルーホール部品も一括処理できるようになります。
ライン構成の簡素化、製造コスト削減、実装品質の安定化などのメリットから、車載ECUやインバータ、コネクタ実装基板などで急速に普及しています。
ピンインペーストの一般的な工程
- はんだペースト印刷
スルーホール部にも十分な量のペーストを供給するため、専用の厚膜ステンシル(3Dステンシル)を使用します。
穴の中にまでペーストを充填できる設計が重要です。 - 部品挿入
コネクタやリード付き部品のリードをスルーホールに挿入。スルーホール用マウンターまたは手挿入が一般的です。
ピン挿入時にペーストが押し出されないよう、ペースト物性や挿入速度にも配慮が必要です。 - リフローはんだ付け
SMD部品と同様にリフロー炉に通し、加熱ゾーンでペーストが溶融し、リードとスルーホールパッドがはんだ付けされることで電気的・機械的接合が完了します。
設計上の技術的ポイント
ピンインペーストは従来のスルーホール実装と比較して特殊な設計要件があります。
以下の点に注意が必要です:
・はんだ量の確保:
スルーホール内とパッド部の両方を満たすには、通常のSMDより多量のはんだが必要です。
→ ステンシル開口の最適化(スロット形状、3D盛り)や、はんだペーストの粘性・粒度も選定のポイントです。
・リードの形状:
はんだ濡れ性を考慮し、丸ピンやフラットピンなど、ペーストが流れやすく表面積が確保できる形状が望まれます。
・スルーホール設計:
穴径、ランド径、ソルダーレジストクリアランスなどをピン径やペースト粘性とマッチさせることが必要です。
IPC規格(IPC-2221など)に準拠しつつ、適度なクリアランス(例:+0.15〜0.2mm)が推奨されます。
・ペースト落下・ブリッジ防止:
ペーストがピン挿入時に押し出されすぎると、隣接パッドへのブリッジや、実装不良の原因になります。
挿入力・ピン端形状・ペースト粘度のバランスがカギです。
車載コネクタにおけるメリットと適用例
車載用途では、コネクタやシールド付き端子、電源用高電流ピン付きコネクタなど、スルーホール構造が必要な部品が多く存在します。
ピンインペースト技術を活用することで、手はんだ工程の削減・自動化による安定品質の確保・リフロー設備の共通化といった大きな利点が得られます。
ローゼンバーガーでは、ピンインペースト対応を明示したスルーホール製品(例:HFM®、FAKRA、RosenbergerHSD®、H-MTD®など)を展開しており、設計段階での部品選定と製造工程の最適化が可能です。
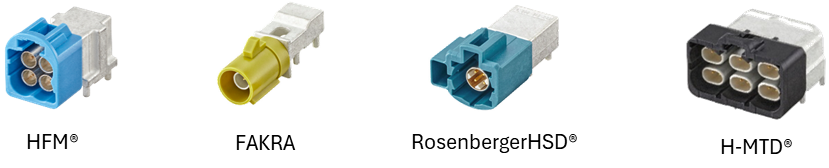
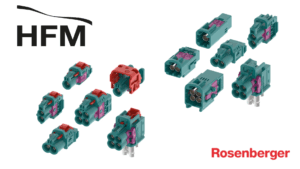
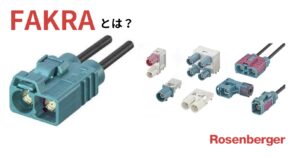
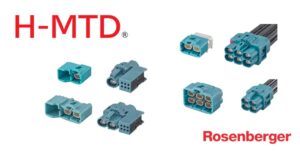
まとめ
ピンインペーストは、スルーホール部品のリフロー実装を実現する高度なプロセス技術です。
設計者にとっては、基板設計・部品形状・はんだペースト仕様・温度プロファイルなど、複数要素を同時に考慮する必要がありますが、実装の一貫性と生産性の向上に大きく寄与します。
車載用途では、信頼性試験(温度サイクル、振動試験、接触抵抗確認など)と組み合わせて、長期耐久性を重視した実装戦略の一環として活用が進んでいます。