自動運転技術やADAS(Advanced Driver-Assistance Systems, 先進運転支援システム)の進化によって、現代の車両には多くのカメラやセンサーが搭載され、大容量・高速・低遅延なデータ通信が不可欠となっています。
4K/8Kカメラ・LiDAR・ミリ波レーダーなど各種センサーから発信される大量のデータを車両内で安定的に伝送するためには、これまで以上に高周波特性とEMC性能を兼ね備えた信頼性の高いコネクタが求められるようになりました。
従来、車載カメラやインフォテインメント用途には、FAKRAコネクタ(シングルエンド伝送)やHSDコネクタ(差動信号伝送)が標準的に使用されてきました。
これらのコネクタは、信号伝送において現在でも十分な性能を提供していますが、通信帯域が6GHzを超える時代に突入する中で、その限界が徐々に明らかになりつつあります。
さらに、複数チャネルの並列化やユニット数の増加、搭載スペースの制約などの要因により、コネクタに求められる要件は単なる伝送性能にとどまらず、小型・軽量・省スペースといった、現代の車両設計ニーズへの対応が必要になっています。
こうした背景を受けて登場したのが、ローゼンバーガーが開発したHFM®(High-Speed FAKRA-Mini)です。
HFM®は28Gbps/20GHz対応の高速伝送性能と当社FAKRA比最大80%の小型化を実現。さらに、360°シールド構造による優れたEMC対策と自動組立てによる高生産性設計を両立しています。
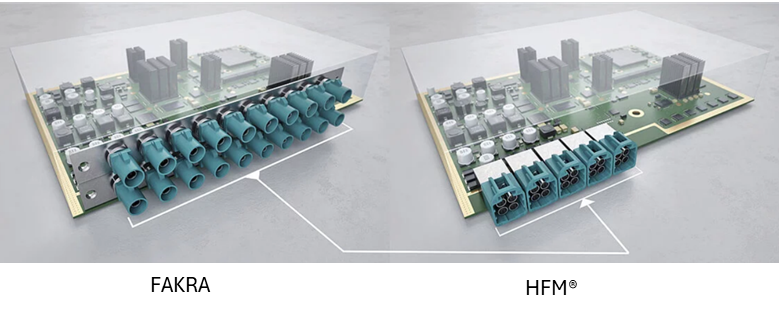
加えてHFM®は、従来のFAKRAやHSDと同様に「USCAR」に登録されており、グローバルで標準化されたインターフェースでもあります。
つまり、単なる“部品”ではなく、自動車業界における通信基盤のインフラ化が期待されている次世代の同軸コネクタと言えるのです。
本記事では、HFMコネクタの技術的特徴、活用メリット、設計・選定時の実践的なポイントを、設計者や調達担当者向けに詳しく解説し、次世代車載ネットワークにおける最適なコネクタ選びの指針を提供します。
HFMコネクタの基本概要
HFMコネクタとは?
HFM®(High-Speed FAKRA Mini)コネクタは、ローゼンバーガーが自動車用の高速通信ニーズに応えるために開発した、次世代同軸コネクタです。
従来より広く採用されているFAKRAコネクタと同様に、標準コーディング12種類を備えた標準インターフェースコネクタです。
HFM®コネクタ開発にあたり、より高い周波性能の確保を筆頭に高EMC性能・高振動耐性・耐環境性など、車載用途に求められる全ての条件を満たす為、端子にはSMP構造を取り入れました。
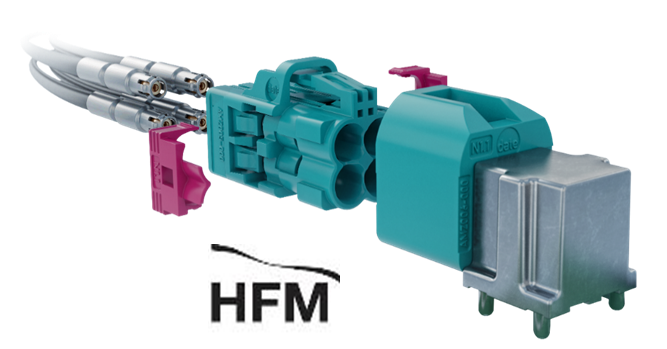
HFM®の主な特徴
・高周波数対応と高速データ伝送
HFM®はDCから20GHzまでの広い周波数帯域に対応し、最大28Gbpsの高速データ伝送を実現しています。
これにより、4K/8K映像信号や大量のセンサーデータを高速・低遅延で伝送でき、ADASや自動運転領域でのリアルタイム処理を支えます。
・コンパクト設計
従来のFAKRAと比較して最大80%の省スペースを実現しています。1極から4極までの多極対応により、複数チャネルの信号を一括で接続可能です。
これにより、配線量や設計スペースを大幅に削減できます。
・高いEMC性能とノイズ耐性
HFM®は360°の金属シールド構造を備え、優れたEMC対策を実現しています。外部ノイズの影響を受けにくく、各種EMC試験にも適合する高い信頼性を提供します。
エンジンルーム周辺や車内の高ノイズ環境でも安心してご使用いただくことが可能です。
・高い信頼性と耐久性
FAKRAはSMB構造をベースに設計されているのに対してHFM®ではSMP構造を採用し、高周波領域でのリターンロス(反射損失)やインサーションロス(挿入損失)を最小限に抑制。
また、LV214・USCAR-49といった車載規格にも準拠しており、温度変化・振動・湿度といった過酷な環境下でも高い信頼性と耐久性を発揮します。
・自動組立てによる効率的な量産性
HFM®は金属の構成部品をすべてプレス加工品(板金部品)で統一しております。これにより、量産における生産コストの低減と組立精度の向上、
また連続端子による供給が可能になることで自動組立プロセスを実現しています。
・豊富なラインナップによる柔軟性
HFM®はモジュール設計を採用しており、1極から4極までの多極構成や防水仕様、水平・垂直タイプなど、多様なバリエーションを展開しています。
これにより、車両の設計要件やスペース制約に応じた最適なコネクタ構成を実現できます。
下記はラインナップの一例となります。その他、CPA(Connector Position Assurance)を兼ね備えた製品や、電源ピン追加タイプ、嵌合音対応品もございます。
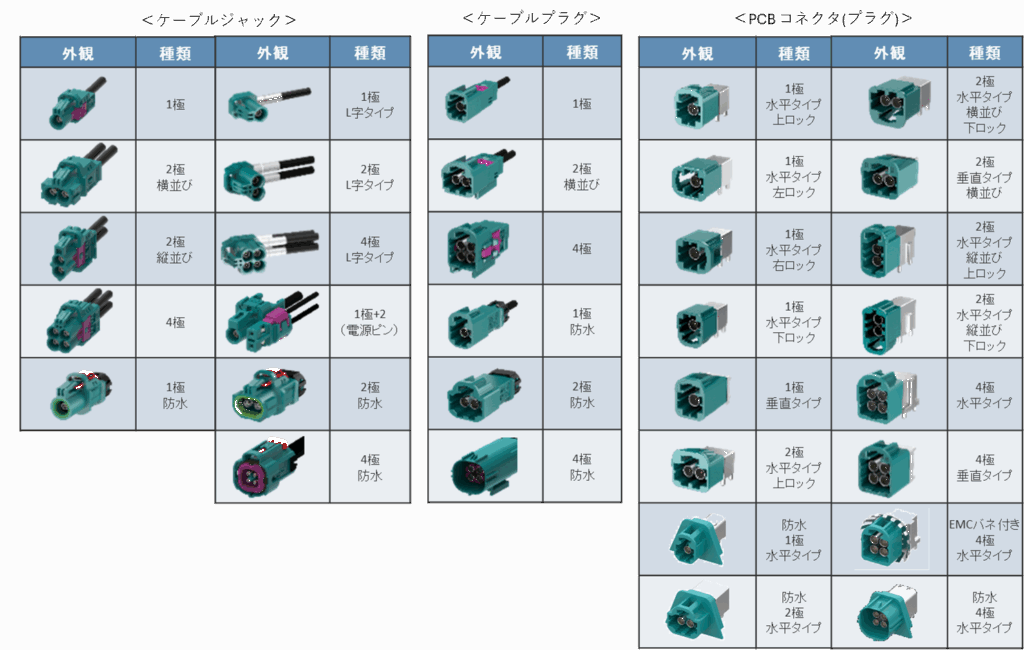
HFM®の基本電気特性
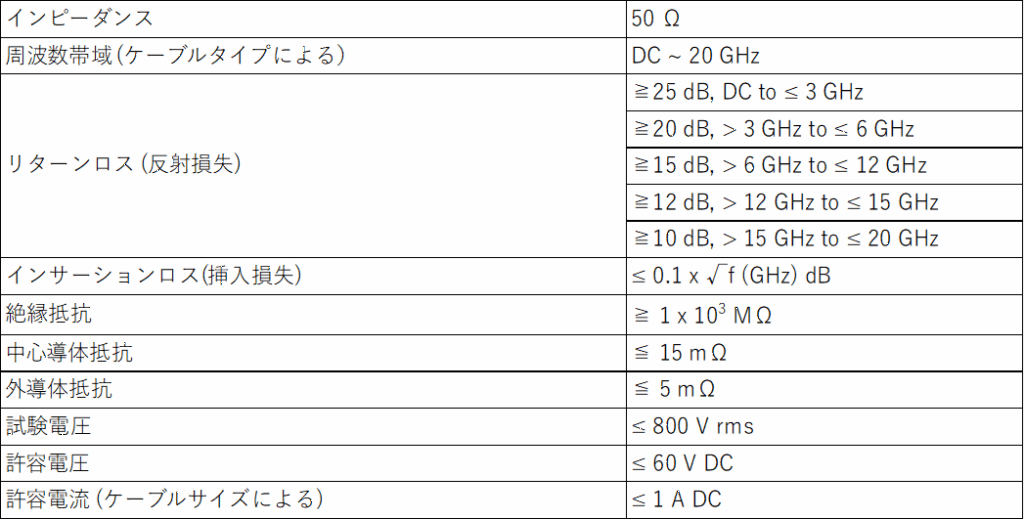
HFM®の主な用途と対応可能プロトコル
HFM®は、以下のような高帯域・多チャネル・信頼性が求められるシステムでの使用を前提に設計されています。
主な用途
■ ADAS(先進運転支援システム)・自動運転
LiDAR、カメラ、ミリ波レーダーなどのセンサーからの高解像度データ伝送に対応。
低遅延かつ信頼性の高い通信が求められる制御系ネットワークで活用。
■ 高精細映像システム
4K/8K対応の高解像度カメラや後席ディスプレイへの映像伝送に最適。
インフォテインメントやサラウンドビューなど、エンターテインメント性と安全性の両立に貢献。
■ ECU/ドメインコントローラ間通信
車両内の複数ECU間、またはECUとドメイン/ゾーンコントローラ間の差動通信に対応。
高速かつ安定したデータリンクにより、Zonalアーキテクチャへの展開にも適合。
■ V2X/5G・WiGig通信
外部通信機能を担うV2Xアンテナモジュール、5G、WiGig(Wireless Gigabit, 60GHz)などの高周波無線通信インターフェースにも対応可能。
対応可能なプロトコル例
■SerDes
・APIX®
・FPD-Link
・GMSL™
・MIPI® A-PHY℠
・PCIe®
・USB
・GVIF
・HDBase-T™
・ASA Motion Link
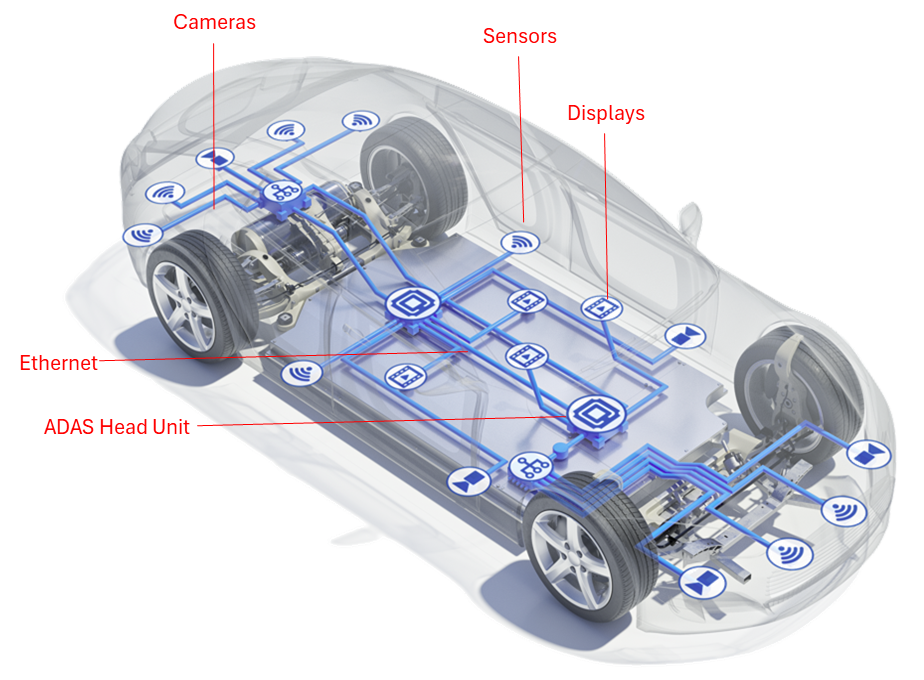
HFM®のインターフェースについて
HFM®インターフェースの標準化は、単なる部品共通化の枠を超え、「車載インフラ全体の共通基盤」を構築するという産業的な意義を持ち、自動車業界全体に以下のような大きな利点をもたらします。
ローゼンバーガーは、HFM®をFAKRAやHSD®と同様に、USCAR-49に正式登録されたグローバル規格として設計・推進しており、これにより以下の多面的な効果が期待されています。
■ 世界共通仕様による普及促進と設計効率の向上
FAKRAの成功事例と同様にHFM®が世界的に統一されたインターフェース仕様となることで、自動車メーカー様およびTier1メーカー様はコネクタの仕様を共通化でき、部品調達や設計の効率化が可能となります。
特に、次世代車載ネットワークに求められる高速・大容量通信においては、国や地域を問わないグローバル調達体制の構築に貢献し、拠点横断的な設計や開発期間の短縮、部品点数の削減を実現します。
■ 異なるデバイス間の接続性向上
標準化されたHFM®インターフェースにより、異なるメーカーやサプライヤー製のECU・カメラ・センサー間でもシームレスな接続が実現します。
ハーネス設計や治具設計の共通化が進み、設計ミスの削減、検証工数の簡略化、さらに開発の柔軟性向上につながります。
■ BCP(事業継続計画)リスクの低減
HFM®のような標準インターフェースを採用することで、特定メーカーの独自仕様に依存しない部品調達が可能となり、自然災害や地政学的リスク、サプライチェーン停滞などの非常時においても、他メーカー製品へのスムーズな切替が可能です。
この柔軟な供給体制の構築は、BCP(事業継続計画)の観点から非常に重要であり、自動車メーカー・Tier1の安定生産体制確保に大きく貢献します。
■ ECU評価・検証作業の効率化
HFM®をECUや各種制御ユニットに標準採用することで、機種ごとに異なるコネクタ仕様であることに起因する評価・検証作業が不要になります。
試作品から量産機種に至るまで同一のインターフェースを用いることで、設計・試験・量産移行までの期間短縮や開発コスト削減が可能となります。
特に複数車種を横展開するプラットフォーム設計においては、この標準化の恩恵は顕著に現れます。
標準化インターフェース(HFM®インターフェース)採用時の注意点
他の標準化されたコネクタと同様、HFM®のインターフェース仕様が公開され標準化されているのはあくまで「物理的嵌合部の形状」に限定されており、電気的・環境的性能に関してはコネクタメーカーごとに大きな差異があります。標準化のメリットを享受するためには、以下の点に十分な注意が必要です。
■ 電気性能・防水性能の違いに注意
HFM®の嵌合形状は標準化されているものの、接点の設計(形状・圧力)、シールド方式、メッキ材質、接触抵抗設計などにより、各社の電気特性・EMC性能・防水性能には大きな違いがあります。
高周波伝送性能(Sパラメータ、インサーションロス、リターンロスなど)や、耐環境性、嵌合作業性、防水等級、組立性などは一律ではなく、実力値の確認が重要です。
■ 粗悪品・コピー品のリスク
近年、公開されているインターフェース形状だけを模倣した粗悪な互換品が市場で散見されます。
これらはUSCARや各種SerDesの要求仕様として規定される電気性能・防水性能を満たさない場合が多く、実車搭載後に通信性能NG、接点腐食、異常温度上昇などの不具合を引き起こすリスクがあります。
■ 異なるメーカー品の混在使用に関する課題
異なるコネクタメーカー製のHFM ®コネクタ同士での嵌合は物理的に可能ですが、接点形状や圧力、めっき仕様の違いにより、電気接続の信頼性や防水性能が劣化する可能性があります。
嵌合自体は成立しても、長期信頼性、環境耐性の担保が困難となり、また不具合時の責任範囲が不明確になるという大きな課題があります。
メリットとして述べたBCPリスク低減観点においても、コネクタの両方(プラグとジャック)をセットで切り替えることを前提としており、異種メーカー同士の嵌合とは区別されるためご注意ください。
推奨事項
設計初期段階において信頼できるコネクタメーカーを選定し、設計書に明記することが重要です。
通信性能においてはSパラメータ・インサーションロス・リターンロス・EMC特性等の実力値確認を必ず実施し、必要に応じて各社の検証データを取得ください。
異なるメーカー品の混在使用は原則避け、やむを得ず組み合わせて使用する必要がある場合は十分な評価試験を実施したうえで、保証内容を明確化することが重要です。
HFM®を採用するメリット
設計空間の自由度を高めるコンパクト設計
HFM®は従来FAKRAコネクタと比較して最大80%の省スペース設計を実現しています。たとえば、複数の高速通信チャネルを1つのモジュールで集約できるマルチポート構成(最大4極)により、制御ユニットやハーネス周辺の部品密度を抑えることが可能です。
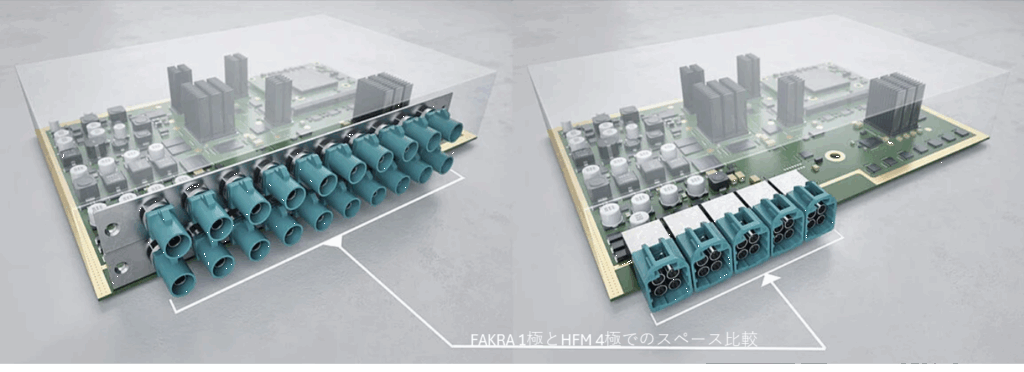
さらに、ストレート・ライトアングルの端子形状、ケーブル引き出し方向、標準コーディング色による視認性など、組込み設計上の自由度も大幅に向上しています。
高信頼性を支える材料・構造技術
接点は金属プレス品による多点接触構造を採用し、またシールド部は亜鉛ダイキャスト製で360°全面カバーをしております。
これにより、高速伝送時の挿入・反射損失の良化に加え、車載コネクタに要求される熱・振動・湿気といった複合環境にも耐える長期信頼性を担保します。
また、嵌合保持力・接触抵抗・温度安定性にも優れるため、ISO 20860/LV214の振動・温度試験に適合します。
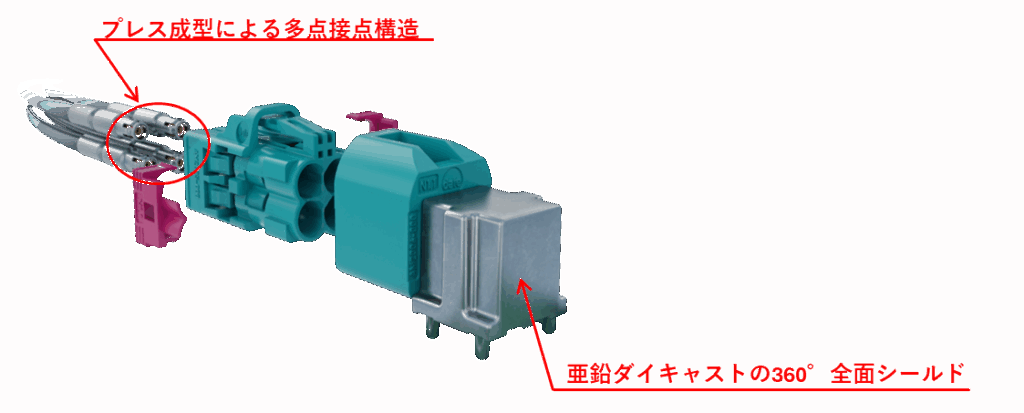
高周波設計、コネクタ選定に対するアプローチ
■ SI設計へのデザインインサポート
HFM®を活用したシステム開発において、SパラメータベースでのSI評価は欠かせません。
ローゼンバーガーでは、推奨レイアウト、高周波シミュレーションのための暗号化3Dモデル、コンポーネント、チャンネルのSパラメータファイルを提供することで開発設計をサポートいたします。
■ EMC設計との整合性
HFM®の360°フルシールド構造を最大限に活かすためには、アースポイントの設計が重要となります。特に、車体接地との電気的連携や、ケーブル側のGNDとの整合性を確保することが求められます。これにより、ノイズの逃げ道を適切に設けることができ、高周波帯域におけるEMC性能を効果的に発揮します。
コネクタ、ケーブルとしては IEC 62143-4-7に規定されるチューブ・イン・チューブ法 (Tube in tube method)により、遮蔽減衰特性を行っています。
■実装とハーネス引き回し
実装に対しては、推奨フットプリントを提供し、また種々の実装・ケーブル方向のコネクタを提供することによりコネクタ挿抜方向に対する干渉回避に貢献します。
またCPA(Connector Position Assurance)機構を持った製品も展開しており、嵌合不良検知・半嵌合によるケーブル抜け防止が可能となり、生産ラインでの嵌合品質にも貢献します。
■測定アダプター・評価用ボードの提供
HFM®コネクタは、開発段階での通信性能検証をスムーズに進められるよう、各種評価用ボードや測定ツール類を提供しています。
実機評価前にEMC試験 (IEC 62153-4-7) や高周波特性検証を行うことができ、設計・検証工数の削減することが可能です。
試作フェーズでは、期待されるパフォーマンスを検証 するために、測定用アダプターの準備 が必要となります。 測定精度を向上させるためには、最小限の挿入損失 と 最適化された反射特性を備えた高精度アダプターの選定が重要となります。
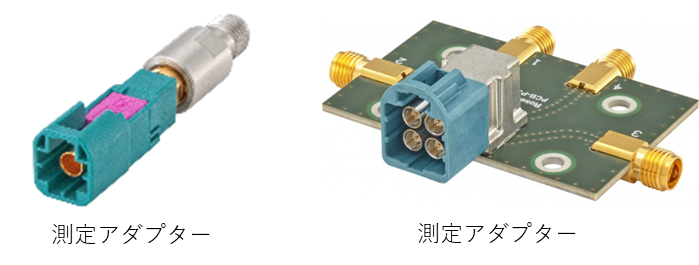
HFM®のアッセンブリ最適化と製造プロセス対応力
HFM®は性能だけでなく、生産現場における“扱いやすさ”にも焦点を当てて設計されています。
■プレス部品主体による量産対応力
接点部品はすべて板金加工(プレス品)を採用しております。切削加工不要なため、コスト競争力と加工精度を両立しています。
また品質が安定し大量生産が可能となるため、グローバル供給の安定性を実現しています。
■ 自動化・柔軟な生産体制への適合性
ハウジングと端子が分離設計されており、アプリケーター(圧着機)の交換だけで多品種対応が可能となっています。
特殊工具も不要で、既存の量産ラインを活用することが可能です。
また、品番統一により部品点数削減と調達管理の簡素化も可能となっています。
■ 製造工程における導入メリット
特殊な冶具や制御装置が不要なため、量産立上げ期間を大幅に短縮することが可能です。
また段取り替えにかかる時間やコストも最小化されています。
既存量産ラインを活用できるため、同一ライン上で多仕様への対応が可能となり、設備稼働率を最大化することに寄与します。
このように、HFM®は現場の実装負荷を軽減しながら、グローバルでの同時展開や設計共通化にも貢献する、まさに“インフラ向け製品”として最適なコネクタです。
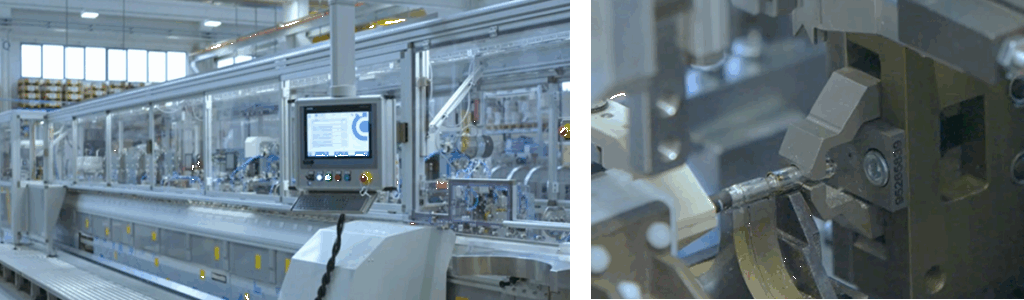
他方式との比較とHFM®の優位性
従来のFAKRAやHSDコネクタと比較した場合、HFM®は次のような明確なアドバンテージを持っています:
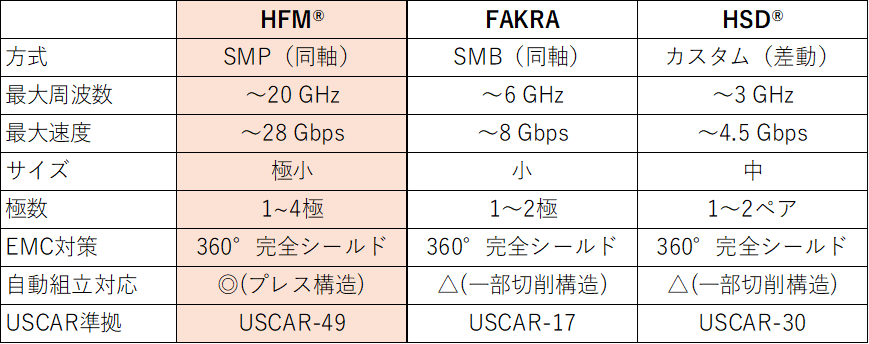
今までも述べてきた通り、特に注目すべきは量産対応力と高周波伝送性能の両立です。
したがって、HFM®は設計者・調達者・生産現場の三方にとってメリットのある、合理的な選択肢となります。
まとめ|HFM®は車載通信の未来を担う新たなスタンダード
ローゼンバーガーが開発した次世代同軸コネクタ「HFM®」について、その技術的な優位性、設計や実装における具体的メリット、さらに生産性や標準化の観点まで、多角的に解説してきました。
今、自動車業界では、ゾーナルアーキテクチャ(ゾーンアーキテクチャ)やSDV(Software Defined Vehicle)などを背景に、車載通信の高速化・大容量化・信頼性向上と同時に、省スペース化・設計共通化・サプライチェーン強靭化が急務となっています。
HFM®は、まさにその要件をひとつの物理インターフェースで実現できる、極めて高性能かつ実用的なソリューションです。
■高周波・省スペースに対応した次世代コネクタ
- 最大28Gbps/20GHz対応の高速伝送性能
- FAKRA比最大80%の小型化による省スペース設計
- SMP構造による優れた挿入・反射特性(Sパラメータ実測保証)
- 360°シールド構造による高EMC性能
- プレス部品による高生産性と自動組立対応
■グローバル標準としての産業的意義
- USCAR-49に準拠した国際標準インターフェース
- コネクタ仕様の共通化による設計・調達効率の向上
- プラットフォーム開発・Zonal設計への適合性
- グローバル調達によるBCP体制の強化
■多面的な導入メリット
- ADAS・自動運転における高信頼性通信の実現
- ECU間・ドメインコントローラ間の差動高速伝送
- 4K/8Kカメラ、V2X、5G、WiGig等への対応
- MIPI A-PHY、FPD-Link、GMSL™、HDBase-T™など各種プロトコルへの適合
■標準化の恩恵と注意点
- 世界共通仕様により、設計の共通化・部品調達の効率化・開発期間の短縮を実現
- 異なるメーカー間の機器接続が可能となり、ECUやセンサー間の互換性が向上
- BCP対策として、特定メーカーに依存しない柔軟な調達体制を構築可能
- 標準化は物理嵌合形状のみで、電気・環境性能はメーカーごとに異なる点に注意
- 片側のみの混在使用や粗悪な模倣品は信頼性劣化や不具合の原因となるため要注意
■設計支援と量産対応力
- 推奨フットプリント・Sパラメータ・評価用アダプターの提供
- EMC設計支援・ノイズ対策設計との整合性の確保
- プレス部品の採用によるコスト最適化と安定量産体制 自動化対応構造・品番統一によるライン負荷の軽減と工程効率化
最後に
HFM®は、単なる「高性能コネクタ」にとどまらず、車載システム全体を横断的に最適化できる“標準通信基盤”としての可能性を秘めています。
自動車の進化がソフトウェアで加速する今、HFM®のような柔軟かつ強靭な物理インターフェースは、ますます重要な役割を担うことでしょう。
ぜひ、貴社の次期車両設計において、HFM®の導入をご検討ください。ローゼンバーガー・オートモーティブ・ジャパンへのご相談をお待ちしております。